美国制桶工业的工艺技术情况简介 1、制桶工业概况 美国制桶企业的共同特点是产品品种比较单一,年产量大,工厂人员较少。典型的5家企业情况如表1所示。
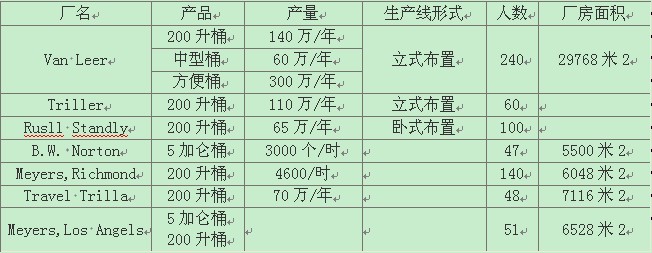
2、制桶工艺 (1)、钢板剪裁 美国制桶厂全部采用冷轧卷板及开卷设备。开卷机组由开卷机、矫直机、测量和导向系统以及剪切机组成,对卷板进行开卷、校平和剪切。剪切后桶身板材精度,要求对角线误差±1毫米。 桶底盖的开卷机组与冲压机床相串联。 (2)、磨边 剪切后的钢板通过自动喂料机进入磨料机,磨边效率一般而言并不太好,但由于是冷轧钢板,所以问题并不大。美国的磨边机钢板的输送速度是无级调速的,另外砂轮的转速也是可调的(2000~4000转/分,应用调速电机),还配有每磨300张钢板可自动调节砂轮进给量3‰英寸(0.076毫米)的装置。 砂轮一般为1英寸宽,磨热轧板时2英寸宽,较为特殊的是磨镀锌板时使用4英寸宽的装有弧状砂布的磨轮。 (3)、焊缝 美国的钢桶厂焊缝已普遍采用自动缝焊机,而且多数是美国CARANDO公司生产的,型号较多。自动缝焊机由卷圆、送桶、焊接、压平等机构组成,卷圆仍为三辊,被卷成形的板由于挡板的阻挡而套在上部,而后被送桶链送往焊接电板轮处,电极轮通过Z字槽分出的两部分与变压器的两级相接,焊接后,焊缝还正处在红热状态时,即通过压平辊,使焊缝平整、密实。 焊机有直流和交流两种,直流焊接功率因数高,较省电,但冷却要求较高;交流焊接功率因数低,较费电,但冷却要求较低。焊机夹持桶身的形式有两种,一种为漏斗形,用3~6个大凹面轮子定位,适用于单一桶型的生产,若更换品种则需更换轮子,较为费时,同时要求桶身板材尺寸也较严格。另一种为褶缝型,桶身是用两排斜轮和两对压紧辊固定,特点是直径变化时调整较为方便,缺点是如果调整不好(斜轮顶不实),容易使搭边过小形成废品。 CARANDO公司的缝焊机在供电方式上均已采用次级整流供电方式,取得了更佳的电效率和稳定的焊接电流。至于三相供电式的产品,据介绍由于采用工频供电的电效率太低,目前尚无较为成熟的产品。 CARANDO公司生产的1424-1型自动缝焊机的主要技术特征是:供电方式:单相交流,功率:200千伏安,生产率:900个/小时,焊接钢板厚度:0.6~1.5毫米。该公司其他类型的自动缝焊机,可供参考的焊接参数为:二次电流20,000安培,二次电压交流时4.97~8.7伏,直流时2.93~5伏。 另外该公司也生产1200只/小时的高速焊机,采用单相次级整流的供电方式。 (4)、翻边与涨筋 翻边机采用模具挤压法,翻边均匀一致,功率高,较之滚压法质量好。涨筋机亦用锥面结构涨筋,两道筋分别先后涨筋。这两台机器均是用机械(偏心、连杆)方式工作,维修方便。 美国VANLEER公司和TRILL公司采用了数控立式成形生产机组,它是一种新的多工位的特殊组合机床,这一机组突出的优点是具有较高水平的自动化和工艺适应能力。它采用美国ALLEN-BRADLEY公司的可编程序控制器控制。修改、调整工艺参数和部分产品规格,只需用几秒钟变换控制程序就能实现。 另外立式成形机组在机构设计上,摆脱传统的框框,采用更灵便的传动机构,例如采用直流伺服电机,滚珠丝杆和槽轮杆件机构等大大减少了设备的运动惯量,因而能以较低的能耗,获得更高的运行速度,各工位的平均生产速度可达到每小时生产800只200升钢桶的水平。同时工位之间的传送,改变了卧式生产线链式输送的传统方式,采用支持式的刚性输送带,缩短了生产流水线,定位精度大大提高,结合采用挤压翻边、整边的工艺,获得高质量的桶框翻边,为优质的封口提供了可靠的保证。 (5)、封口 封口机有的采用卧式双动,卷封仍沿用二道轮,其轮和盘的材料均为合金钢,经热处理和磨削后才使用。卷封处的填充剂均采用橡胶类乳化型填充剂,填充剂的充填多数在封口时喷入;也有先预喷,经烘干后再封口的。封口时常常同时往卷封轮上喷洒冷却剂以利延长使用寿命。 美国用于化工等液体危险品包装的标准200升钢桶,一般不再采用双重卷边封口,而是采用应力集中现象不明显的圆形卷边为主。由于这类卷边优越的力学结构,具有较强的抗冲击能力,在芝加哥曲勒(TRILL)公司参观时,为我们表演的45°坠落试验,高度标定为2.4米,三重圆形卷边的钢桶都没有出现破损渗漏现象。 美国采用的圆形卷边以三重卷边技术专利为主,采用底、盖预卷边。预喷涂密封填料的工艺。底、盖预卷边的工艺是先在一设备上将桶底盖预卷一个小圆弧状小边,然后再到封口机上卷封成桶。 当然,这种卷边对桶身的翻边尺寸要求较高,一般宽度误差应控制在±0.25毫米以内,这也是目前国外普遍采用挤压成形式翻边机的重要原因之一。 (6)、试漏 试漏机与国内所用的形式区别不大,只是卧式两端均有丝扣,能调整测试的长度,以求对中,这在国内尚未见使用。 (7)、表面处理(脱脂、磷化) 桶身和桶底盖成形后,各厂均进行表面处理,而且均有磷化部份,设备均呈隧道型,一般为脱脂、水洗、磷化、水洗、烘干等几部分,脱脂、磷化、水洗均采用喷淋式,传动为单排,链传动。桶身、桶盖有集中处理的,也有分开处理的。 烘干形式与内外表面喷涂的烘干形式相同,一般烘干长度与脱脂、磷化、水洗的长度相当,表面处理工艺有关参数如表2。 表2
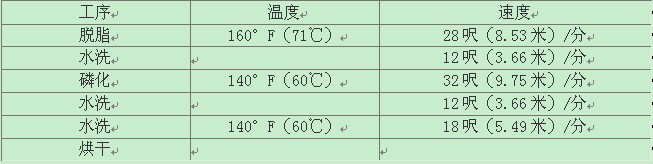
(8)、内表面喷涂 所有喷涂设备有卧式和立式两种,卧式和国内方式区别不大,立式在国内尚未见到,其特点是减少桶位置的变化。方法是夹持器将到位的桶举起,在往返过程中喷涂即结束。喷涂是采用无气喷涂的方式。另外,二涂一烤或二涂二烤较为普遍。烘干大多采用天然气并伴有热风循环的方式,此法烘干效果很好,也有一个厂采用煤气燃烧明火加热的办法,此法国内也有采用,估计热效率不及热风循环的高,烘干炉未见使用气幕,想必用热风循环的办法,会有效地防止热量的散逸。 烘干炉一般设计温度350~450°F(176~232℃),烘烤时间15分钟。 (9)、外表面喷漆 采用无气喷涂方法,所有设备亦全为卧式喷涂机,该机与国内的机械喷涂机不同点是所用喷枪很多,桶身设有三把喷枪,桶盖每侧各有两把,喷枪数量多能缩短喷涂的时间。 外表面喷漆的烘干炉,至少能烘干两排桶,这样桶的耗热量能降低,烘干方式和内表面喷涂的烘干方式相同,对聚脂类漆烘干温度为350°F(176℃),时间10分钟。 (10)、印铁 美国万里(VANLEER)工厂设有三条印铁线,分别印大、中、小型桶,其中200升桶的印铁较为罕见。印铁机是套色印刷,所以制做后的桶十分精致,印好的铁板,经焊接,成形仍无脱落,表面处理后也无影响,当然成品桶还要有焊缝的外涂工序。 3、材料利用 美国国家标准(ANSIMH2.1——1997)规定普通200升钢桶底盖和桶身分别采用不同级别的钢板。底盖为20级(0.823毫米以上),桶身为18级(1.09毫米以上),这是从力学的等强度概念制定的标准,在材料利用上有很大的经济意义,每只桶约可节省6.6%的钢材。 另外,底盖落料采用宽幅卷料,交错排列,大大减少了边角料的浪费,它比原来窄幅卷板单排排列的落料方式,大约可以节省5.4%的钢板。 4、螺圈组装 闭口钢桶的螺圈组装,国内工厂一般是由以下三道工序完成:1、冲孔;2、孔拉伸;3、锁装。而在美国我们见到了美国法兰公司提供给制桶厂的一次组装专用模具,采用一道工序完成大、小螺圈的组装。在芝加哥曲勒公司和休斯敦腊希.斯特赖公司所见的实际使用情况都是令人十分满意的。 5、填料的应用 填料的种类主要有以下两种: (1)、740HS发泡型填料,布累斯公司(DAREX)生产,成型条件为110℃,13分钟;每只底盖用量12.5克,采用高压无气涂装,底盖自转速度0.7秒/转。 美国万里、曲勒等公司使用的这种填料,成型后在桶底盖预卷边缘部形成一个环形密封垫圈,保证了桶的抗渗漏性能。 (2)、以合成橡胶为主的乳胶填料,牌号为DA-REX60,W.R.GRACE公司生产,胶凝条件为常温。根据现场观察验桶结果,封桶成功率在99.9%以上,说明以上两种填料在美国的应用已有成熟的经验,其技术性能可予信赖。
|